Швейцарские электрички понравились белорусам, а руководство компании отметило перспективность восточноевропейского рынка, поэтому уже в 2013 году в Фаниполе был построен завод «Штадлер Минск» общей площадью 220 тыс. кв. м, из которых 35 тыс. кв. м занимает производство. Сегодня на предприятии работает более 500 человек.
Как это сделано: поезда
Любой вагон начинается со специальных алюминиевых профилей.
«Они приезжают сюда уже готовыми, поскольку панели такого размера производят лишь четыре поставщика в мире», — рассказывает Филипп Бруннер, директор ЗАО «Штадлер Минск».
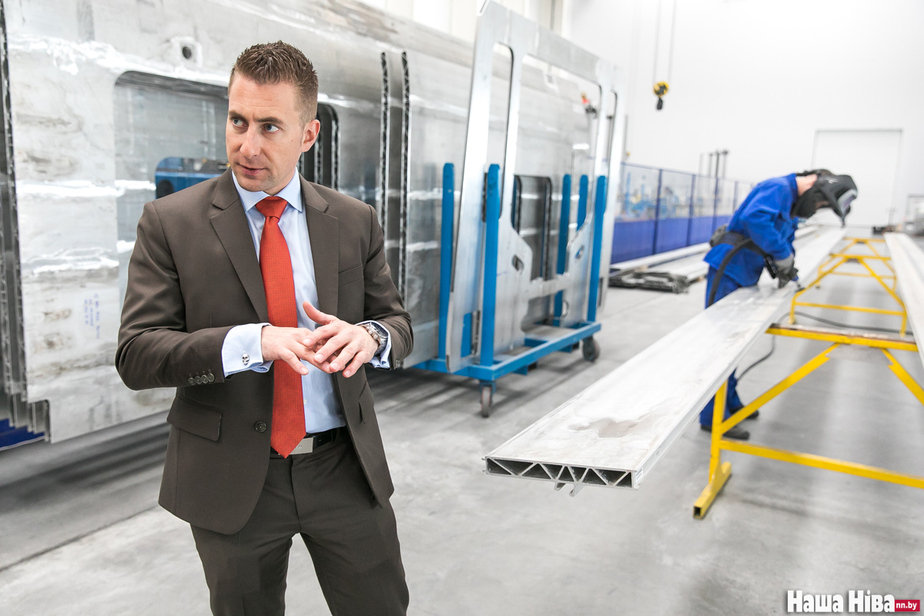
На «Штадлер Минск» осуществляется полный цикл сварки. Здесь есть стапеля на каждый тип вагона для сварки крыши, основания, боковых и торцевых стенок, перегородок и множества других элементов. Процесс всегда одинаков: от поставщиков приходят профили, рабочие их подготавливают, устанавливают в стапель, фиксируют с помощью пневматических и механических устройств, после этого дополнительно фиксируют точечной сваркой. После этого элемент готов для «обварки» сварочным роботом.
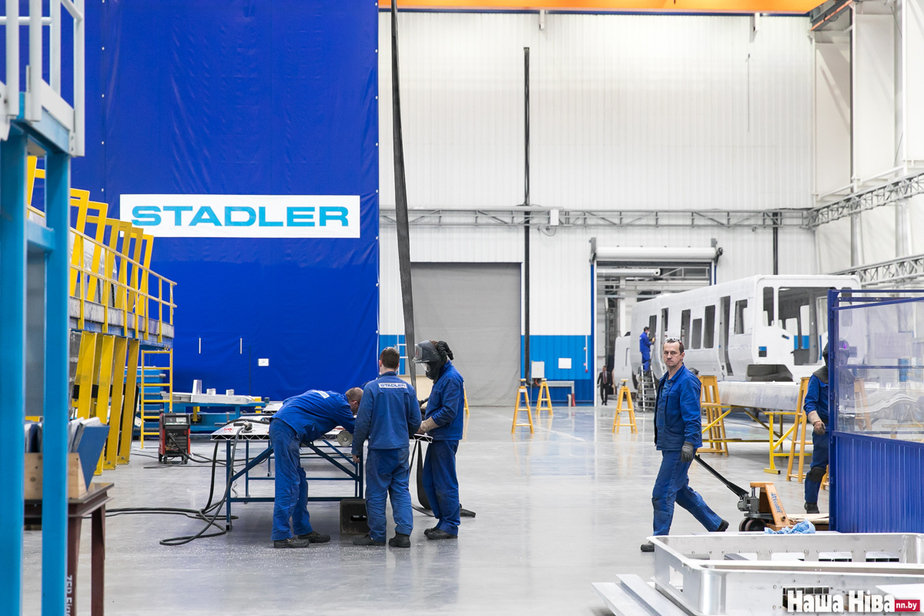
Следующий шаг — механическая обработка станком, который по разработанной в соответствии с технической документацией программе обрабатывает все элементы. Станок может работать с 14 различными инструментами и постоянно их менять, обрабатывая объект в соответствии с техническими требованиями. Он делает все необходимые вырезы, многие из которых впоследствии станут дверями и окнами.
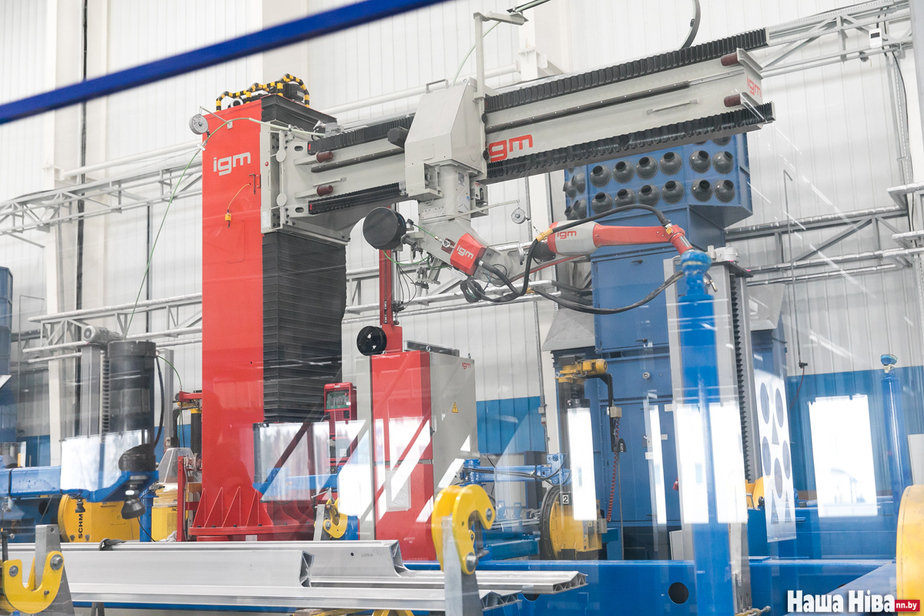
После этого, бывает, снова необходима сварка роботом (например, если имеются маленькие элементы, которые входят в состав более крупных). Затем, сразу после механической обработки станком или повторной сварки, готовые элементы устанавливаются в главный сварочный стапель.
Качество сварки проверяется лазером в 250 точках на поверхности кузова. Помимо того, каждый десятый вагон проходит рентгеновский контроль на качество сварочных швов.
После полной сварки и контроля качества вагона он попадает в дробеструйную камеру, где все части кузова, на которые впоследствии будет наноситься краска, под давлением обрабатываются мелкими камешками. Таким образом поверхность вагона становится матовой, что улучшает сцепление краски с металлом.
Следующий этап — грунтовка. После этого проводят окраску вагона в камере и сушку при заданных температуре и влажности, что гарантирует высокое качество. На некоторые модели наносится 12 слоев краски! Процесс длительный: занимает от двух до трех недель.
После полирования вагон отправляют в сборочный цех, где работники сверлят те отверстия, которых не сделал робот. Всего таких мелких отверстий в каждом вагоне более тысячи. Затем происходит монтаж внутреннего оборудования: электроники, обшивки, окон, сидений и других компонентов.
Следующий этап — установка вагона на тележки. После этого он уже готов к испытаниям, которые проводятся на собственной электрифицированной линии протяженностью около 2 км на территории предприятия. Два-три месяца уходит на изготовление одного вагона. За год производственные мощности предприятия позволяют производить около 150 алюминиевых вагонов и 100 стальных секций (это, например, 35 поездов и 30 трамваев).
На этот вопрос Филипп Бруннер ответил вполне однозначно: белорусские.
«Некоторые поезда, которые вы сейчас видите, мы выпускали в Швейцарии, когда этот завод еще только строился. Но теперь поезда производятся в Беларуси, поэтому, без вопросов, это «Made in Belarus».
Например, трамваи, которые мы сейчас производим для Санкт-Петербурга, являются полностью белорусскими. Часть проектной документации нам помогали разрабатывать наши швейцарские коллеги, но все же 80% было сделано в Беларуси. Большинство материалов для их производства мы закупаем тоже здесь. Кстати, именно белорусскими будут и поезда для минского метрополитена, первый из которых мы планируем выпустить уже во второй половине 2018 года», — рассказывает Филипп Бруннер.
В настоящее время на предприятии заканчивают сборку последнего из 23 трамваев по заказу из Санкт-Петербурга. Там они уже бегают и даже пришлись по вкусу как пассажирам, так и транспортникам.
Трамваи от «Штадлер» — «умные»: их автоматизированная система контроля пассажиропотока следит за его интенсивностью через камеры, установленные как внутри салона, так и на внешней поверхности транспортного средства. Вся информация о ситуации на дорогах, количестве пассажиров поступает в центр управления в депо, где она анализируется, после чего вычисляется оптимальное количество транспортных средств на маршруте.
«На территории предприятия — электрифицированная линия на 27 кВ, 3 кВ и 650 В, что позволяет нам полноценно испытывать любую нашу технику. Протяженность линии небольшая — около двух километров — но этого достаточно для проверки работоспособности», — рассказывает Владимир Русак.
Вот как выглядит полностью готовый для отправки в Санкт-Петербург трамвай, модификация которого («Метелица» В85300М) в желтом цвете проходила испытания на минских маршрутах в течение некоторого времени.
Двери открываются только после нажатия на соответствующую кнопку. Это непривычно пассажирам, но полезно, поскольку помогает сохранять тепло внутри вагона, ведь бывают ситуации, когда на остановке один-два человека, и нет смысла открывать одновременно все двери.
В настоящее время на предприятии работает более 500 человек: как местных, так и из других городов. В ближайшее время планируется значительно увеличить производственные мощности предприятия. Уже в 2018 году компания трудоустроит дополнительно 200 человек, а в следующем году — еще 200. Средняя зарплата здесь, по словам представителя компании, «выше среднего по стране».
«Штадлер Минск» экспортирует свою продукцию далеко за пределы Беларуси. Наши поезда и трамваи востребованы в России, Азербайджане, Грузии, Норвегии. Кроме того, на предприятии производят комплектующие для компаний группы Stadler в Германии, Польше, Чехии.
Источник: nn.by